Chapter 17: Finish
Finishing will typically make your bow lose a few pounds of draw weight. I started off a couple pounds heavy and finished off just above the target weight.
To start off, get rid of any tool marks with your scraper. You can sand them off too but typically the scraper is faster. After that, I sand the whole bow with 220 grit sandpaper. I don’t like to use anything courser than that since you’ll leave tool marks.
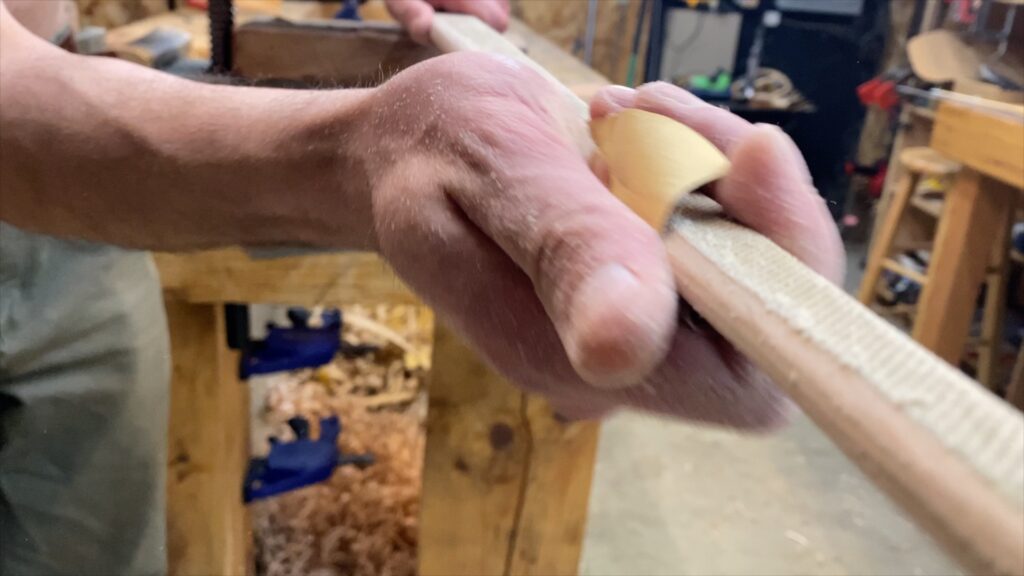
After sanding a layer, I wipe down the bow with a wet cloth. It should be dry in a minute or two. If you’re in a real hurry you can use alcohol and it will dry pretty instantly. This step will raise any wood fibers that have been lying flat, and will make sure they get shaved clean in the next step.
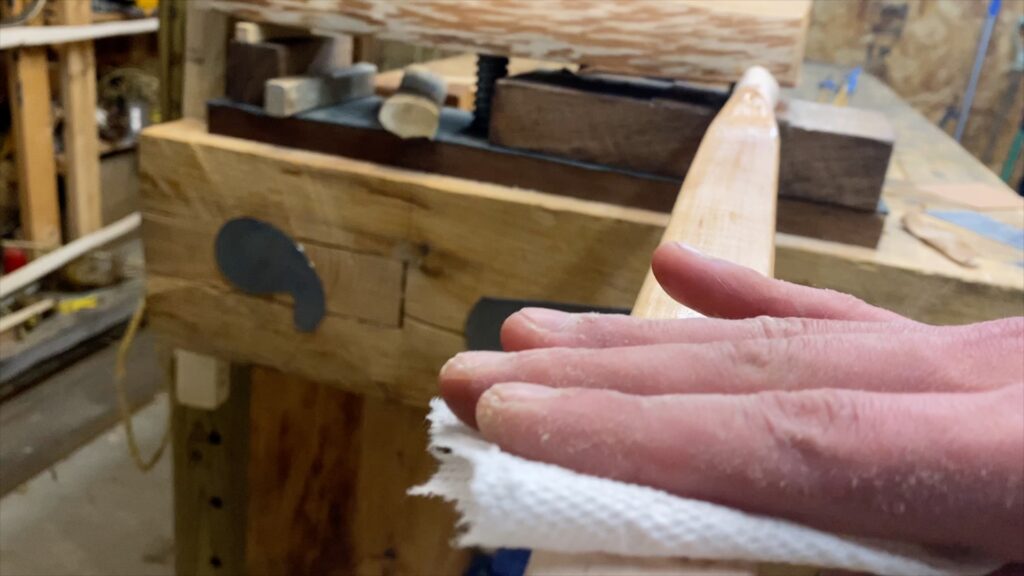
Sometimes I’ll give the bow a second pass with 220 grit, if things are still looking rough. This time I went straight up to 320. If you’re planning to stain your bow don’t sand any finer than that. I like to stop at 300, otherwise the stain will go on in a patchy way. The courser grits let the stain penetrate more evenly.
When I don’t want to stain a bow I’ll keep sanding with finer and finer grits, up to around 1000 grit, using the wet wipe to raise the grain in between each grit.
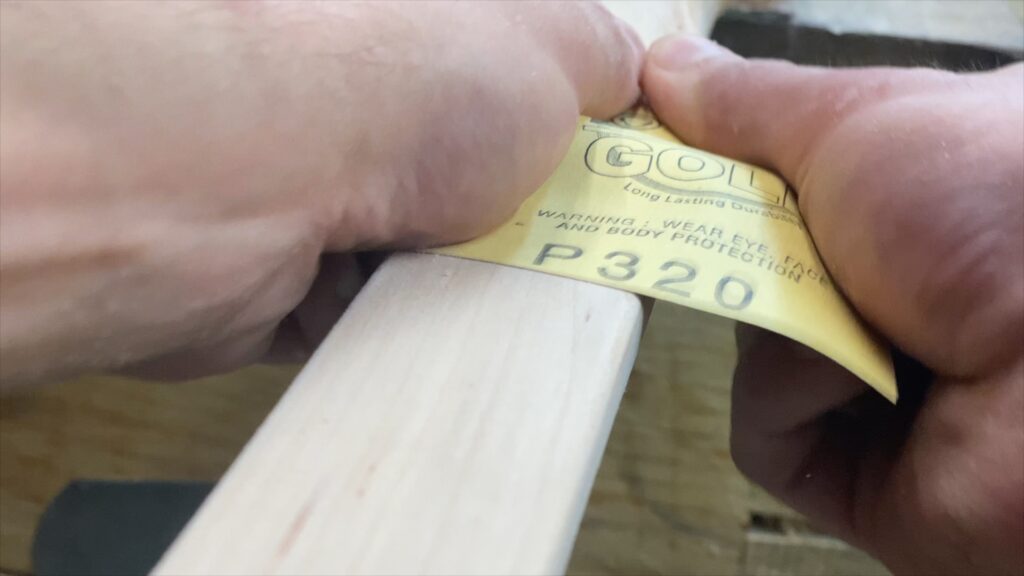
Here I’m using leather dye, this is feibings dye, I’m using the colors Black as well as Saddle Tan. You can also use any other wood stain or mix your own analine dye. I like leather dye because its easy to control and blends well.
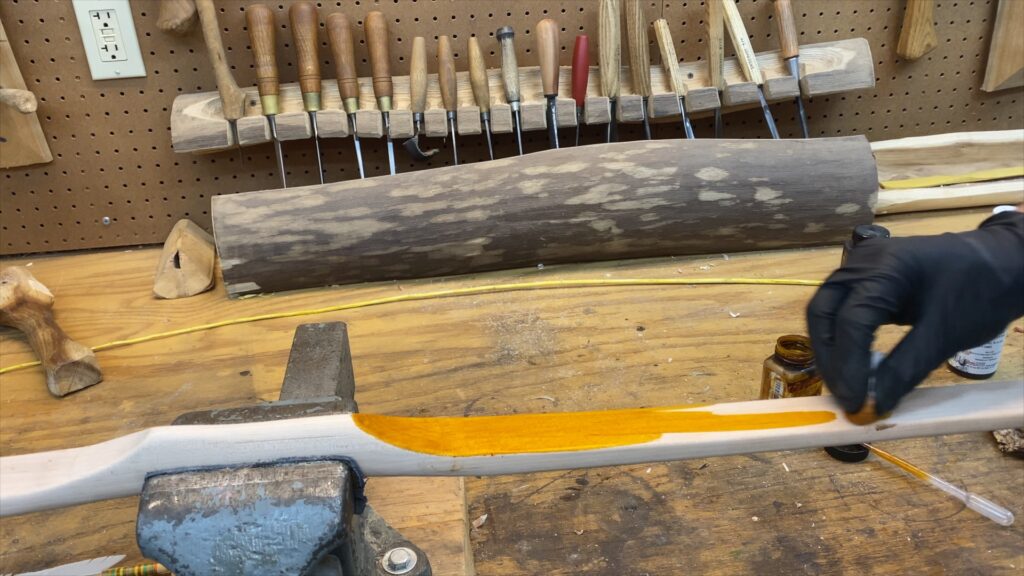
I coated the whole bow in saddle tan, then covered the back in black, and finally I blended the tips and handle into black.
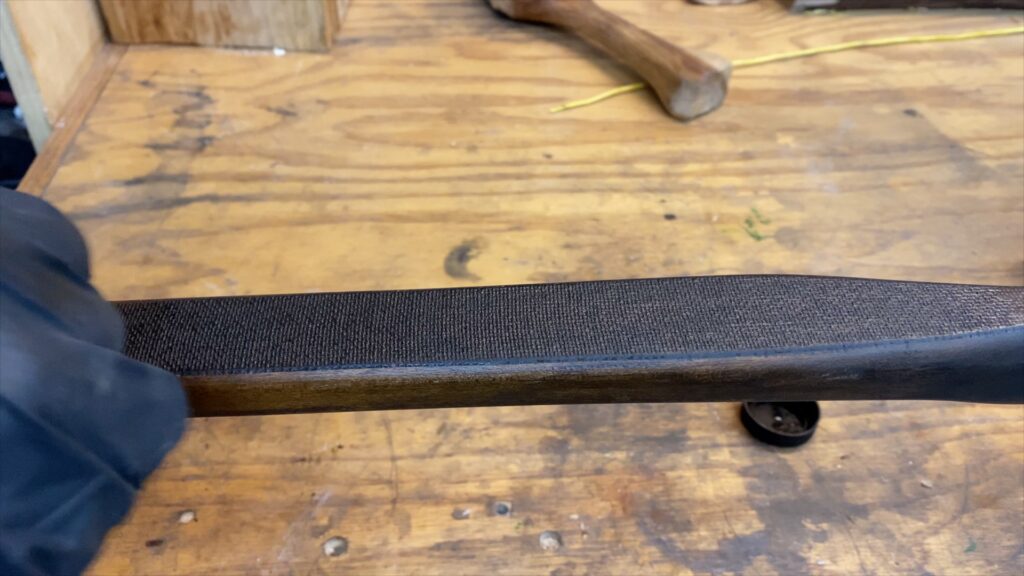
I’m using a cotton ball wrapped in gauze, but you can also just use a bit of paper towel or a pom pom brush if you have one. Make sure the brush is pretty dry or you’ll get a sloppy effect. If you have too much stain loaded then offload some until you get a light streaky effect. It’s worth practicing on scrap before giving it a go.
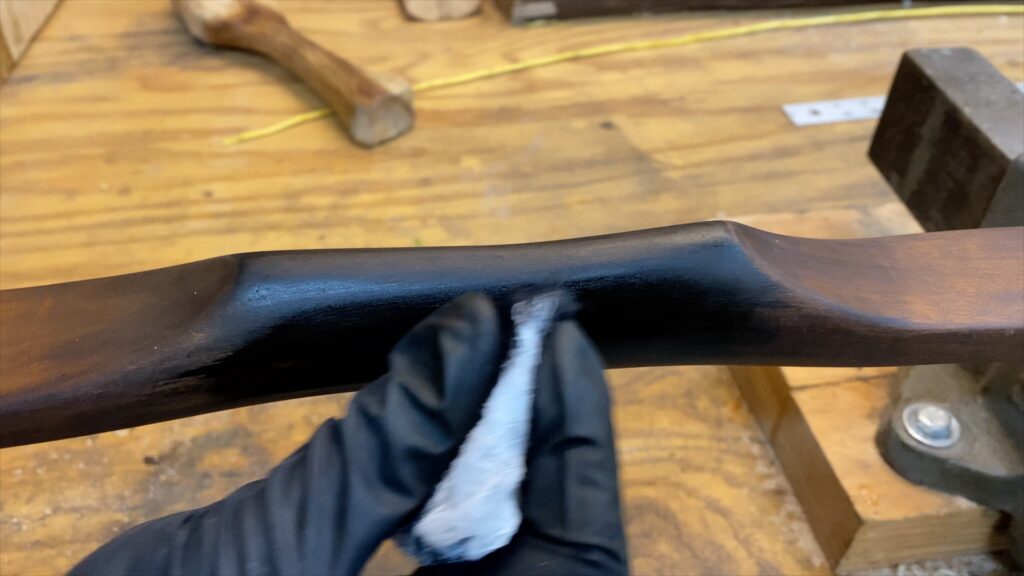
After everything is dry we’re ready for finish. I really like shellac, its my go to finish. I buy the flakes and mix it myself, it’s easier and cheaper that way. Spray shellac is also a great choice since it dries so quickly. I don’t recommend buying pre mixed shellac in cans because a lot of it is sold expired, and there’s not good way to check if you have a fresh can.
Usually 3-7 layers of finish is enough. The last few layers should be polished if you don’t want any bumps from dust.
You can also use your preferred polyurethane finish, or most other finishes. If you have gunstock finish those are some of the best choices. Tru oil is a lot of work to put on but probably the finest finish I’ve used. And of course you can use a drying oil like linseed or tung oil. Personally I would only use these on an unstained bow.
Finally I like to buff the bow with a coat of beeswax. If you do this make sure it won’t interfere with your finish, in case you ever have to patch the bow. Otherwise you’ll have to clean it all off. Shellac is very versatile and one of few finishes that plays well with wax
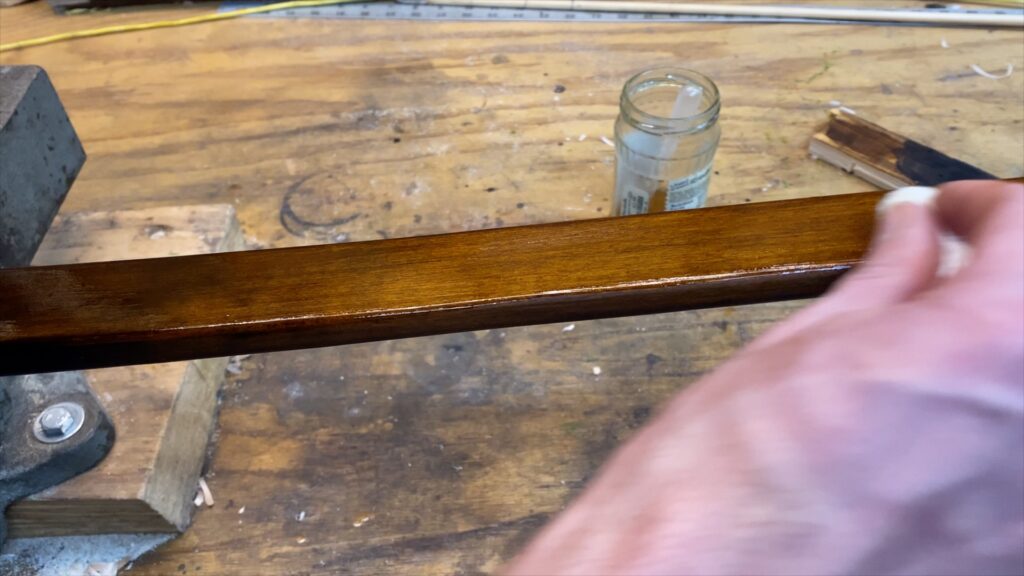
Mervyn Patterson
Hi, congratulations on your full tutorial.It was very well done,easy to follow and understand,one of if not the best tutorial I have seen.Thanks very much I as a amateur bowyer found it most informative but being English my experience is more toward the English Longbow or D section bow.I have had some success with Italian and Pacific Yew.After seeing this I will have a go at a flat bow.
Best wishes Mervyn Patterson UK.
dansantanabows
Thanks Mervyn. In the UK also keep an eye out for Ash, Elm, and Hazel. On facebook there’s a UK bowyer’s group you may want to check out. There’s probably someone close to you who can show you the ropes. There are also several UK bowyers on the other groups and r/bowyer. Good luck and enjoy the journey!
Duke
I am very new at this and can’t wait to start. thank you very much for these easy-to-follow instructions and video. As soon as I obtain the equipment and a good piece of wood I will try to follow your directions.
thanks again and be safe
dansantanabows
Glad to hear it Duke. Hope to see your bow on r/bowyer one day. Good luck and feel free to post as many tiller checks as you need
Gingdah
I enjoyed the detail that you have. This one of best Detail videos on making a bow I seem.
Tyson
Picked up a red maple board and a draw knife today, getting started this weekend. Can’t thank you enough!
dansantanabows
That’s awesome! With red maple I’d go for a slightly wider bow than I have, maybe 2” wide, or a slightly lower draw weight of 30 or 35 pounds. Next time if you can, try to get one of the maple species categorized as a ‘hard’ maple like sugar maple. Silver and red are a bit less dense, but don’t worry and it won’t stop you from making a bow. Just pay extra attention to the set and drop off the draw weight if you start seeing more than a couple inches.
Good luck and feel free to post as many tiller checks on r/bowyer as you need
Tyson
Thanks, Home Depot was my first stop for lumber, red maple was the best they had in hardwood planks at the moment, excluding mahogany. I did notice the porousness so went with the best most dense board I could find. I’ll post my progress!
Terry Bowmam
I am not able to get bow wood boards around here to sort thru.
I can get Black Walnut or Eastern Red Cedar bow making lumber, but requires a backing. I don’t want to waste my hickory backing yet, been a long time simce I made a wooden bow.
My question is, will that linen backing in your video be strong enough, with some reflex? Or maybe double it?
Thanls
dansantanabows
I’m not a big fan of doubling up on the backing because of the extra mess and glue line. Better to use a thicker backing from the start. I think with ERC lumber you’re probably going to need a hard backing unless you find a miraculously clean and straight board. With natural staves, if you’re able to chase or almost chase a ring then ERC can handle being unbacked, despite the popular advice. The problem is that the other popular advice for ERC is that it’s ok to violate the fibers on the back. This is only true to an extent and I wonder if this practice has much to do with juniper’s reputation for breaking in tension.
John Halverson
You would NOT be wasting your hickory backing on an Eastern red cedar board (so long as the board is fairly decent grained with few or no knots). In fact, Hickory backed eastern red cedar (often called HERC) is considered a superior combination for high speed, high efficiency bows.
dansantanabows
I will write more in the future as my formal ideas develop. My informal ideas are easily found on r/bowyer. Thanks for this backhanded compliment, I think.
Pat
I’m impressed, I must say. Seldom do I encounter a blog that’s equally educative and amusing, and let me tell you, you’ve hit the nail on the head.
The problem is something which too few people are speaking intelligently
about. I’m very happy I stumbled across this during my hunt for something concerning this.
Kevin
G’day Dan, fantastic tutorial. I have always wanted to make a bow and I would like to thank you for putting the time into your channel. I live downunder and I am trying to work out what local timber I can use. After watch this I think I will try to practice on a fine grained timber and will certainly look what is in town at the hardware as well. Thanks again. Cheers Kev
Rex
G’day Kevin, I’ve heard quite a few say Spotted Gum is a good option of you find a nice board. I couldn’t find any it the right size at my local timber supplier so I opted for a really straight bit of Jarrah as it’s properties looked similar to hard maple (density, elasticity and modulus or rupture), hopefully it will work. Some others have said iron bark could work for a bow, but that stuff is so hard it makes it difficult to shape.
Rex
G’day Kev
I’m keen to try this out as well. I’ve heard Spotted gum is a good option. I’m going to try it with some Jarrah. Ironbark might work but that stuff’s really hard, shaping it will probably be a pain and lots of tool sharpening.
Cheers,
Rex
Rex
G’day Kev
I’m keen to try this out as well. I’ve heard Spotted gum is a good option. I’m going to try it with some Jarrah. Ironbark might work but that stuff’s really hard, shaping it will probably be a pain and lots of tool sharpening.
Cheers,
Rex
Mickey O'Neill
Dan–My son and I have decided at the same time to get into traditional bow-making. We shot off and on for years, and really enjoy being out in the fresh air and sunshine losing arrows together!
We both truly appreciate your teaching style and the beauty of the videos you’ve made. Thanks for your generosity!
We both went to the store and got red oak boards for our first bows. That is some hard wood! It’s pretty slow going for the moment, but we’ll see how it goes as we progress.
We share the ultimate goal of crafting character bows out of wood we harvest for ourselves. We’re in Oklahoma, and tried over 20 years ago to make a bow from a piece of Osage Orange. Our attempt still hangs in my office! Hopefully, with your tutelage, we will produce something that shoots!
dansantanabows
Good luck Mickey! I heard from your son on reddit last week and am very glad to hear you’re taking on the project together. Let me know if you have any questions or trouble, and feel free to post as many tiller checks on reddit as you need. Go make a bow!
Ross H
Dan, I loved this tutorial. Extremely helpful, a friend of mine and bowyer, Correy Hawk pointed me to your video. I had a question regarding the scale of the bow.
If I wanted to follow your tutorial to make a kids bow (for a 3-5 year old) how does this scale down from the longer ones you make?
Thank you.
dansantanabows
Correy is an awesome bowyer and teacher. I would love to film one of his classes someday. To answer your question it depends a lot on the design. The absolute easiest way is to copy other kids bow’s dimensions that you see on other forums. Of course you can only copy the rough out dimensions since the true dimensions will be revealed by tillering. For a same length bow you can adjust the draw weight by scaling the width. And as a rough rule of thumb you can estimate the bow length by doubling draw length and adding on the length of your stiff handle, and adding a few extra inches per limb for stiff tips. This will give you plenty of margin for error. It’s possible to make a bow shorter but that will give you a nice safe length.